|
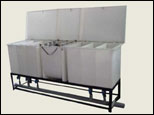 |
CONSOLE
OF TANK
|
Console of Tanks for convenient
and compact usage. A console of 7 Tanks
is used comprising Pre- Rinse and Post-Rinse
Tanks together with the main Lacquer Tank.
These Tanks are normally fabricated out
of Polypropylene and are provided with Lids
to ensure the dust free condition of the
solution when not in use. A common drainage
system is often provided.
|
|
|
|
|
|
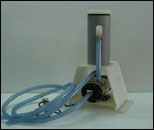 |
A
CARTRIDGE FILTER
|
A Cartridge Filter of 2
to 5 microns mesh size is recommended for
filtration and removal of dust particles.
This serves the dual purpose of Filtration
as well as movement of the solution.
|
|
|
|
|
|
|
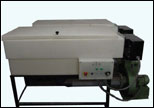 |
HOT
AIR BLOWER UNIT
|
After the coating is completed
on the pieces, they are required to be blow
dried, which ensures removal of excess drops
of Lacquer as well as increases the temperature
of the articles before they are taken for
Oven curing.
|
|
|
|
|
|
|
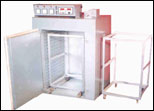 |
CURING
OVEN
|
After blow-drying the coated
pieces are required to be cured in an air
circulatory oven. The articles are required
to be cured at 160 Deg. C for 20 minutes.
The pieces may be either loaded on the Trolleys
for convenient handling or loaded in the
Oven in any suitable manner.
|
|
|
|
|
|
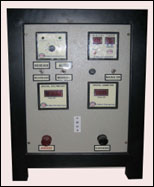 |
RECTIFIER
|
This is a special Rectifier
of capacity ranging up to 100 Volts and
20 Amps. The capacity required depends upon
the number of pieces loaded in any batch.
The Rectifier consists of ramping arrangement
for gradual increases of the voltage, Digital
Timer and Digital Meters. The Dimmerstat
should be motorized with a Contactor arrangement.
|
|
|
|
|
|
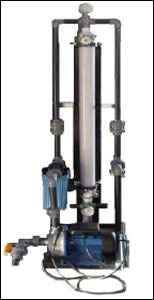 |
|
ULTRA
FILTER
|
An Ultra Filter Unit is
required in this process for the removal
of water-dissolved impurities from the bath.
This Unit consists of a Membrane of suitable
capacity, high-pressure Pump and inlet outlet
pipes. The Unit is conveniently mounted
on Angle Frame.
|
|
|
|
|
|
|
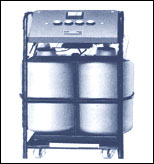 |
|
D.M
WATER PLANT
|
A suitable capacity D.M.
Water Plant is recommended so as to get
water of less than 5 microsiemens.
|
|
|
|
|
|
|
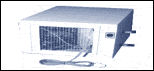 |
CHILLER
UNIT
|
Since this process works
best at temperature around 25 Deg. C, a
Chilling arrangement of suitable capacity
is recommended.
|
|
|
INSTRUMENTS
|
a) pH Meter
b) Conductivity Meter
c) Refracto Meter
d) Magnetic Stirrer ( for Dye Lacquer Plant)
|
|
|